Una dintre marile reușite ale planului Renaulution implementat de Luca de Meo în cadrul Renault Group este introducerea inteligenței artificiale și a digitalizării în aproape toate planurile procesului de dezvoltare, logistică și producție ale vehiculelor. O vizită a Profit.ro în două dintre centrele de dezvoltare ale companiei franceze ne-a dezvăluit cât de mare este anvergura digitalizării pentru compania care deține marca Dacia.
Suntem în Technocentre, Guyancourt, Franța, principalul centru de dezvoltare al grupului Renault, un loc gigantic, în care lucrează mii de oameni și în care sunt gândite, dezvoltate, pregătite de producție autovehiculele grupului. Viața unui automobil începe aici, pe computerele inginerilor și designerilor, de la o idee, și ajunge până în faza de simulare și testare a prototipurilor. În Technocentre am descoperit cât de mare este viteza cu care se lucrează în prezent la procesul de dezvoltare a unui automobil, de zeci de ori mai repede decât se făcea acum 10 ani.
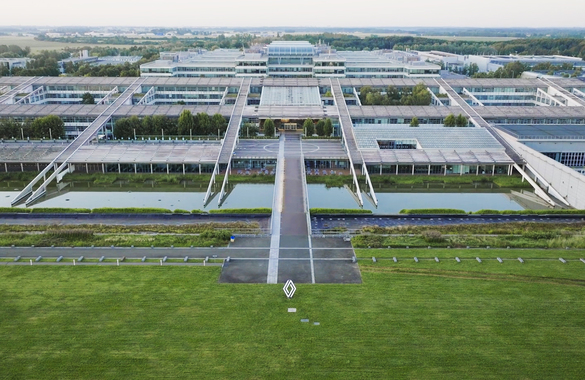
Înainte de asaltul inteligenței artificiale, al realității virtuale și al computerelor de mare putere, automobilele erau create tradițional în toate companiile auto. De la planșa de desen a unui designer, creația se muta în atelierul unui sculptor – modelator, apoi se multiplica în mai multe variante pentru se lua o decizie cât mai bună. Fiecare dintre variante dura luni bune, iar până se ajungea la ceea ce în industria auto se cheamă „concept freeze”, adică forma definitivă a unei mașini, treceau 2 – 3 ani. Doar atunci putea începe procesul de industrializare, adică proiectarea și comandarea pieselor componente la furnizori, testarea prototipurilor și pregătirea producției.
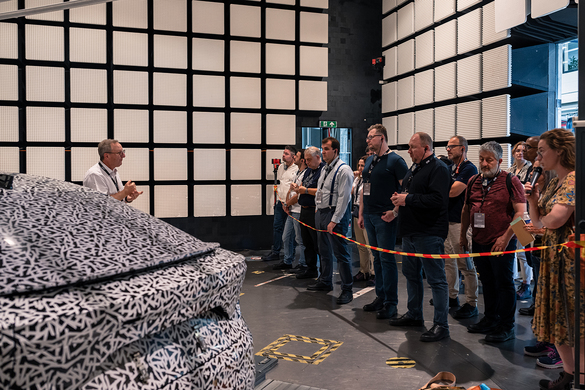
Technocentre este cel mai important punct al rețelei de cercetare și dezvoltare al grupului Renault, a fost inaugurat în 1998 și are 9.110 angajați. Statisticile mai arată că 77% dintre angajații centrului sunt ingineri și manageri. A fost încă de la început punctul central al planului Renaulution, fiind locul din care pornește orice proiect al grupului. După patru ani, planul a adus o puternică digitalizare a întregului proces de dezvoltare, cu implementarea inteligenței artificiale ca tehnologie principală. Cele trei etape specifice industriei auto - upstream, dezvoltare și producția de prototipuri - pornesc aici, în Tehncocentre și sunt conectate apoi cu toate celelalte centre tehnice și de design din lume, inclusiv cu cele din România.
Design AI
Astăzi, ceea ce se întâmplă în centrul de design al Renault ar părea o magie pentru cineva care ar fi capabil să călătorească în timp din anii 90, de exemplu. Stațiile de lucru ale designerilor reușesc să genereze 10 automobile pe zi, iar instrumentele digitale pe care le au la dispoziție folosesc o bază de date uriașă, care include materiale, texturi, culori ce pot fi testate în câteva secunde. „Totul este stocat în cloud, inclusiv modelele produse de noi, într-un sistem securizat la care avem acces doar din acest centru, iar viteza de lucru este foarte mare”, ne spune unul dintre designerii aflați în Technocentre.
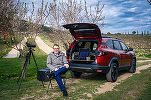
Ni se prezintă una dintre stațiile de simulare și, având la ochi o pereche de ochelari de realitate virtuală, urc într-un șasiu ce sugerează o mașină. Practic, sunt doar scaunele, câteva repere fizice, bord, volan. Odată ce ochelarii VR sunt la ochi, apar brusc finisajele și detaliile mașinii. Este un Renault 5 cu toate elementele sale, suprafețele au prins culoare și viață și pot fi atinse. Este unul dintre simulatoarele pe care cei de la Renault testează materiale, comenzi, butoane, culori pe care designerii le propun. Este un proces extrem de rapid și cu costuri infinit mai mici față de ce se petrecea în urmă cu ani.
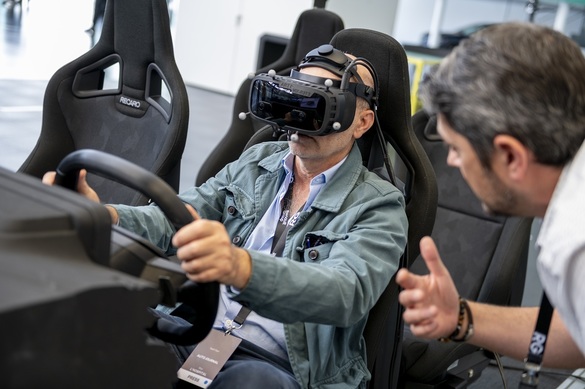
„Avem 5 centre în toată lumea, cu 500 de angajați și 25 de naționalități. Avem un avantaj competitiv mare în fața rivalilor, de exemplu față de modelul VW ID.1 care a pornit odată cu Twingo, exact datorită acestei digitalizări și a inteligenței artificiale pe care o folosim”, ne spune Laurens van den Acker, Chief Designer Officer al Renault Group. Designerul ne lămurește în legătură cu modul de lucru colaborativ din prezent, care permite nu doar creșterea vitezei, ci și lucrul în paralel la etapele care în trecut se efectuau succesiv, secvențial. „Tehnologia nu înlocuiește oamenii, ci amplifică puterea lor creativă”, spune Laurens van den Acker.

Într-o singură zi, trecem prin toate zone de lucru din Technocentre, atât de multe încât încep să se suprapună informațiile. Aflăm cum sunt antrenate computerele cu AI, pentru a putea colecta și utiliza datele necesare. Reușim chiar să vedem cum aplicația de design bazată pe AI creează un concept-car. Pe un ecran sunt implementate câteva instrucțiuni tipice, stiluri de design, repere pe care trebuie să le conțină mașina. În câteva secunde, pe ecran apare o mașină, un coupe stilat, cu linii futuriste. Designerul face câteva ajustări, pentru detalii, culori, apoi vedem forma finală, care pare cunoscută. Este chiar Renault Embleme, studiul pe care compania l-a prezentat public în toamna anului trecut, prototipul unui vehicul de familie cu propulsie pe hidrogen, cu materiale reciclate și foarte prietenos cu mediul.
Câteva ore mai târziu avem deja ocazia să ne urcăm în mașina reală, creată pe computer și transformată în realitate de inginerii Renault. Cu materiale simple, accesibile, cu propulsie electrică alimentată de celule de hidrogen. Dar până acolo am putut vedea întreg procesul de creație al acestui model și al celorlalte automobile ale grupului, inclusiv cele de la Dacia.
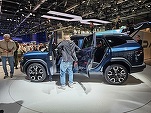
ROADS
Unul dintre elementele centrale ale acestui proces este ROADS, simulatorul uriaș care plutește pe un bloc de beton de 30 de metri și care reușește să reproducă prin intermediul sistemului de pistoane forțele reale din trafic.
Olivier Colmard, vicepreședinte al Renault Group pentru inginerie globală, ne spune că toate aceste simulatoare, virtuale sau reale, au reușit să reducă costurile de dezvoltare cu 53% raportat la ce se petrecea în 2019, iar timpul de dezvoltare a vehiculului s-a redus de atunci cu 25%, doar în această fază. Întreg ecosistemul reușește să simuleze atât vehiculele în sine, cât și sistemele care există în ele și, în același timp, oferă și simularea imersivă, extrem de utilă.
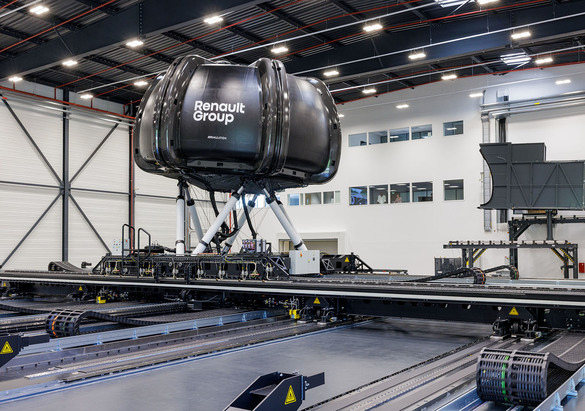
În sala de comandă a ROADS se află câteva zeci de monitoare pe care se văd cifre și imagini video. Dincolo de geamurile sălii, se află hala uriașă în care plutește o mică navă spațială, neagră, pe care scrie Renault Group. Stă pe cele șase picioare, adică pistoanele hidraulice care pot genera rotiri de +/- 180 de grade, cu timp de răspuns de 30 ms. Are 15/15 metri, iar în interior spațiul are șapte metri. Este locul în care este introdusă mașina ce va fi testată, în condiții ce reproduc traficul real. Șoferul este deja acolo, îi vedem reacțiile și gesturile pe monitoare, în timp ce pe alte monitoare se vede mediul virtual în care rulează. Se aud comenzi, inginerii urmăresc cifrele care se derulează pe ecran, în timp ce „naveta spațială” începe să se agite într-o parte și alta. Se rotește, se lasă pe o parte sau pe alta și produce exact accelerațiile specifice virajelor, frânărilor sau accelerărilor.
Și restul de cifre sunt impresionante. Toată instalația are 92 de tone, iar utilizarea ei costă 10.000 de euro pe zi. A fost produsă împreună cu AV Simulation, este unică în industria auto și a fost inaugurată în octombrie 2024. Este deja a treia generație de simulatoare pe care o folosește grupul Renault, după C-Cards, din 1998, CAVE, care este utilizată în România, la RTR din Titu, și XR, care era până acum cea mai avansată.
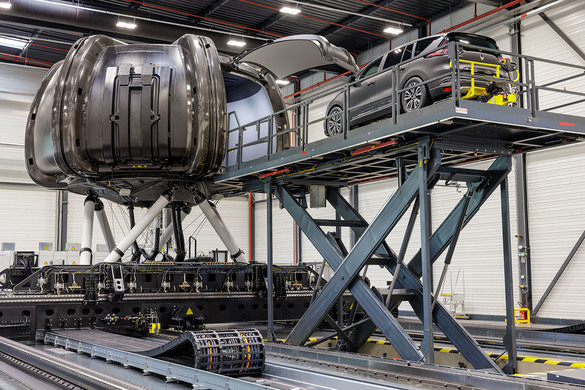
Recapitulăm ce înseamnă toate aceste tehnologii de simulare: costuri mult reduse și timp scurtat la maxim, printr-un design mult mai ușor de realizat și testat, corecții mai rapide ale problemelor constatate și decizii mai rapide la fiecare etapă, reducerea numărului de prototipuri fizice, din nou cu efecte de costuri. Se simulează accidente, aerodinamica, acustica, fiabilitatea și termodinamica vehiculelor. Se simulează comportamentul componentelor, prin gemenii digitali, se simulează sistemele de asistență și software-ul, dar și managementul energiei. Se simulează imersiv automobilul, pentru toate testele necesare înainte de a ieși pe șosea.
Centrul de producție de prototipuri
Puțină lume știe că, la Technocentre, în Franța, există o fabrică de automobile în miniatură, similară unei uzine din viața reală, în care sunt produse doar prototipurile. Linia de prototipuri reproduce fidel secțiile unei uzine de mașini, dar la scară, pentru a se putea testa inclusiv procesele de producție, de asamblare, astfel încât, după validarea lor, acestea să poată fi transferate pe liniile de mare capacitate. Dar aici are loc și montajul tuturor modelelor ce vor fi testate și, uneori, ce vor deveni automobile de serie. Aici am văzut într-un colț viitorul Jogger facelift, am văzut și modele Dacia care erau ferite de privirile jurnaliștilor cu prelate, dar am văzut și prototipurile istorice, care azi sunt deja în producție.
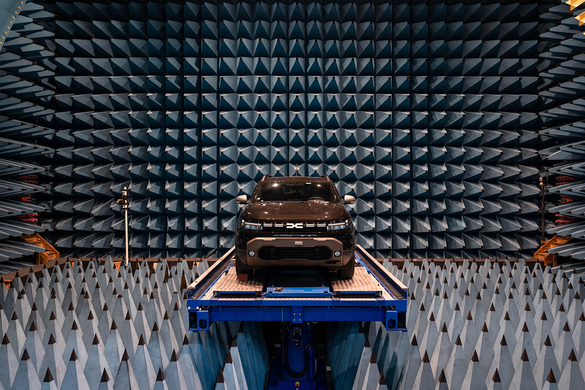
Fabrica de prototipuri are numai 530 de angajați și lucrează cu cele mai noi tehnologii de simulare și testare. Numai anul trecut, centrul a produs 770 de prototipuri, a făcut pregătire cu 500 de angajați de la uzine din toată lumea, a construit 80 de modele de serie și a produs 12.000 de componente prin printate 3D.
Pentru cei pasionați, să spunem că aici au fost construite conceptele Dacia Bigster, prezentat în 2021, și Dacia Manifesto, prezentat în 2022.
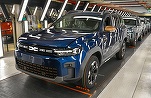
Turnul de control pentru logistică
Înainte să ajungem la Aubevoy, unde se află circuitele de testare ale Renault Group, trecem și prin locul în care inteligența artificială și digitalizarea au intrat în viața celor de la logistică. Este centrul de comandă din care sunt urmărite și controlate cele peste 6.000 de camioane din lume care transportă componente către fabricile Renault și alte 2.000 care livrează vehicule. Pare că a fost gândită de un geniu al logisticii, pentru că îndeplinește aproape orice funcție de care șoferii au nevoie pentru a-și duce piesele la destinație. Scopul principal: livrarea la timp a componentelor, astfel încât nicio fabrică să nu rămână fără piese, nicio linie de fabricație să nu se oprească. Indiferent de problemele care pot apărea în calea unui camion, sistemul alertează și permite aplicarea celei mai bune soluții, indiferentă că e o pană, un război local, un dezastru natural. Vehiculele sunt dirijate către alte destinații, pe alte trasee, ori sunt trimise în cel mai scurt timp alte camioane care să preia marfa. Soluțiile sunt afișate pe monitoare instantaneu, inclusiv cu costurile aferente fiecărei variante, pentru ca operatorul de serviciu să poată lua cea mai bună decizie.
Sistemul a fost instalat în 2024, iar de atunci efectele sunt miraculoase: cu 50% mai puține opriri ale liniilor de producție și economii de 260 de milioane de euro în aprovizionarea cu piese și materii prime. Sunt 25 de fabrici și 22.000 de puncte de distribuție acoperite de acest turn de control, în 114 țări, care grupează 13 platforme logistice.
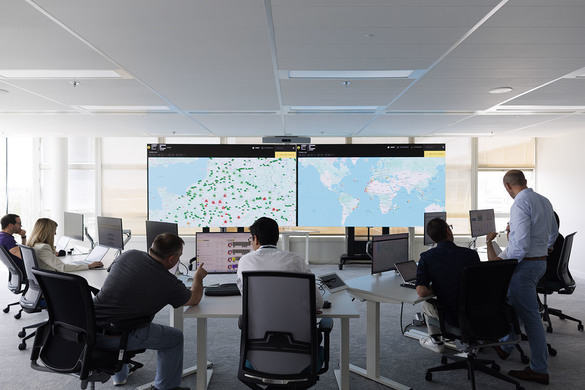
Dar ce este genial la acest sistem este modul prin care sunt anticipate evenimentele cu potențial disruptiv: sunt monitorizate știri din toată lumea, în timp real, cu impact în zona de acțiune a camionului, sunt urmărite buletinele meteo și alte surse de informații și totul este combinat cu monitorizarea prin GPS.
Inteligența artificială analizează toate aceste informații și generează alerte ori de câte ori este cazul. În medie, sunt 50 pe zi, dintre care, în medie, una pe săptămână este considerată gravă și necesită o decizie umană. „Turnurile de control ne permit să avem un răspuns rapid la crize și chiar să le anticipăm, pentru a minimiza impactul și a proteja lanțul de aprovizionare în timp real, oriunde în lume”, explică Sebastien Liorzou, directorul acestui sistem.
Aubevoy – centrul de testare al vehiculelor
Aubevoy este locul în care am văzut, parcate sau circulând în toate direcțiile, o mulțime de mașini camuflate, cele despre care, de obicei, presa scrie când apar pe șosele. Aici, la Aubevoy, Renault testează mașinile înainte de a fi lansate, dar și după ce au ajuns deja în showroom-uri, pentru că actualizarea și remedierea problemelor se face pe toată durata vieții unui vehicule.
Centrul de testare se află în Normandia, la aproximativ două ore de Paris și la puțin peste o oră de Technocentre, și a fost inaugurat în 1985. Este complet înconjurat de pădure, pistele de testare fiind invizibile de pe drumurile publice din zonă, pentru a li se asigura discreția necesară. Aflăm că toate cele 272 de hectare de pădure din jur au fost plantate de companie de-a lungul anilor, pentru că la început acolo era doar teren viran.
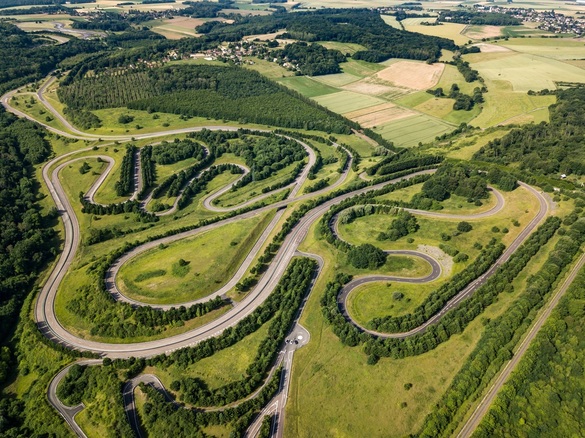
În total, centrul de testare are peste 600 de hectare, 60 de km de piste, inclusiv un circuit de mare viteză, cu secțiunea înclinată, care permite atingerea unei viteze de 250 km/h. Și totul este operat de circa 1000 de angajați. Pistele simulează șosele reale, cu pante, viraje și relief în așa fel încât să fie totul ca în realitate, autostrăzi și zone accidentate.
„Viteza din China acum în toată lumea”, ne spune la centrul din Aubevoy Cedric Combemorel, CTO al Renault Group. Ne explică încă o dată că viteza este una dintre țintele Renaulution, planul lui Luca de Meo, care a însemnat și adoptarea programului Leap 100. Asta a adus reduceri de 16% la timpul de upstream, 41% la dezvoltare și 26% la industrializare. Adică mașini gata de producție în 18 luni și, în cazul noii generații Spring, în 16 luni. Utilizarea AI a redus diversitatea și complexitatea modelelor: din 30.000 de combinații au rămas 1000. Aici, la Aubevoy se încheie, practic, ciclul de dezvoltare, înainte ca mașina să intre pe linia de producție.
Vizităm pistele și zonele de testare a suspensiei, circuitul de viteză, zonele de testare pentru acustică și interferențe electromagnetice. Este un proces cu adevărat complet, care explică și costurile mari ale dezvoltării. Sunt câteva ore pe parcursul cărora vedem mașinile camuflate care trec în toate direcțiile și identificăm printre ele modele lansate deja sau care urmează să fie lansate. Din păcate, telefoanele au fost sigilate încă de la intrarea în centru, așa că rămânem doar cu fotografiile oficiale.
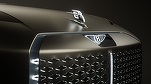
Putem în schimb, în sfârșit, să testăm toată gama de modele a Renault: familia de electrice, Renault 4 și 5, Alpine A290, SUV-urile Rafale, Austral și Espace, dar și Dacia Bigster. Este o ocazie bună să comparăm diferite motorizări și echipări, pe un circuit care te ferește de interferența traficului.
Dar cea mai mare surpriză este testul cu Renault Embleme, conceptul pe care l-am văzut în Tehnocentre în toate fazele de dezvoltare. Mașina este doar un prototip și nu poate fi condusă de persoanele din afara centrului, dar putem vedea cum merge, de pe scaunul din dreapta, în timp ce project managerul Pascal Tribotte conduce pe circuit. Aflăm și scopul acestui automobil, care a așezat Renault pe lista companiilor auto care dezvoltă autoturisme cu propulsie cu hidrogen. „Încă de la primele schițe, Embleme a fost imaginată ca o mașină cu un scop. Trebuia să fie atractivă și funcțională. Ceva ce ți-ai dori să conduci și pe care să-l poți conduce în fiecare zi. A fost concepută pentru a reinventa ceea ce poate fi un vehicul de familie, construită pentru versatilitate, confort, călătorii lungi, aventuri comune și viața de zi cu zi”, a explicat Pascal Tribotte, care ne-a spus că a fost un proiect solicitant, pentru că toate componentele utilizate sunt produse existente în producția de serie.
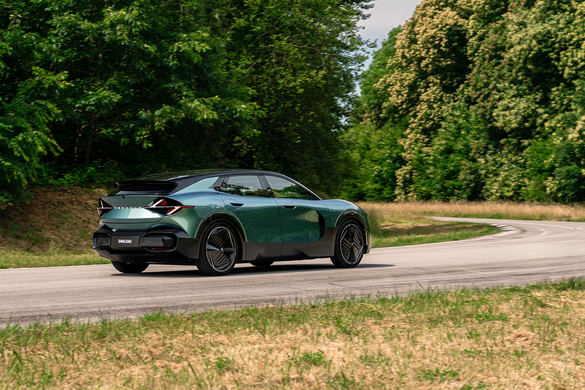
Testul cu Embleme încheie simbolic întreg procesul pe care o mașină îl parcurge în Technocentre și Aubevoy până la faza în care rulează pe șosea. Tehnologiile pe care le folosește Renault în acest moment, atât în Franța, cât și în restul centrelor, inclusiv în România, sunt comparabile și chiar le depășesc din multe puncte de vedere pe cele ale chinezilor și rezultatele ar trebui să se vadă în următorii cinci ani, inclusiv în felul în care se va dezvolta marca Dacia.

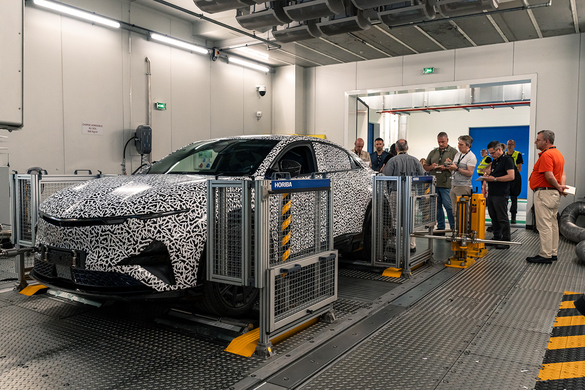